What is OEE (Overall Equipment Effectiveness)
Achieving Excellence with Overall Equipment Effectiveness (OEE)
Overall Equipment Effectiveness (OEE), is the most important metric for evaluating manufacturing productivity. OEE reveals the net productive time in manufacturing, it goes form 0% as the lowest score, up to score of 100% meaning maximum efficiency.
To calculate Overall Equipment Effectiveness (OEE), you need to gather specific data related to your manufacturing process. Here are the key components and the information required for each.
What do you need to calculate OEE
To calculate Overall Equipment Effectiveness (OEE), you need to gather specific data related to your manufacturing process. Here are the key components and the information required for each.
1. Availability
Availability measures the percentage of scheduled production time that the equipment is actually running. To calculate Availability, you need:
- Planned Production Time: The total time the equipment is scheduled to operate.
- Unplanned Downtime: The total time the equipment is not operating due to unexpected stops (e.g., breakdowns, setup and adjustments, etc.).
Availability=( Planned Production Time − Unplanned Downtime ) / Planned Production Time
2. Performance
Performance measures the speed at which the equipment operates as a percentage of its designed speed. To calculate Performance, you need:
- Ideal Cycle Time: The theoretical minimum time to produce one unit.
- Total Units Produced: The actual number of units produced.
- Run Time: The total time the equipment is running (Planned Production Time minus Unplanned Downtime).
Performance=( Ideal Cycle Time × Total Units ProducedRun Time ) \ Run Time
3. Quality
Quality measures the percentage of good units produced versus the total units started. To calculate Quality, you need:
- Good Units Produced: The number of units that meet quality standards.
- Total Units Produced: The actual number of units produced.
Quality=Good Units Produced / Total Units Produced
4. Overall OEE Calculation
Once you have Availability, Performance, and Quality, you can calculate OEE.
OEE= Availability × Performance × Quality
Measure OEE with machines Andon lights
Using Andon lights to measure OEE (Overall Equipment Effectiveness) can streamline the process of data collection and help identify real-time production issues. Here's how you can utilize the Andon light signals for calculating OEE:
Andon Light Definitions:
- Blue: Equipment is on but not running (Planned Downtime or Standby).
- Green: Equipment is running smoothly (Normal Production).
- Orange: Equipment is running but with issues affecting performance (Minor Stops or Reduced Speed).
- Red: Equipment is stopped due to issues (Unplanned Downtime).
Using Andon lights to capture data simplifies OEE measurement. By recording the time intervals for each light signal and correlating them with production data, you can effectively calculate Availability, Performance, and Quality, leading to a comprehensive OEE score. This approach provides real-time insights into production efficiency and helps identify areas for improvement.
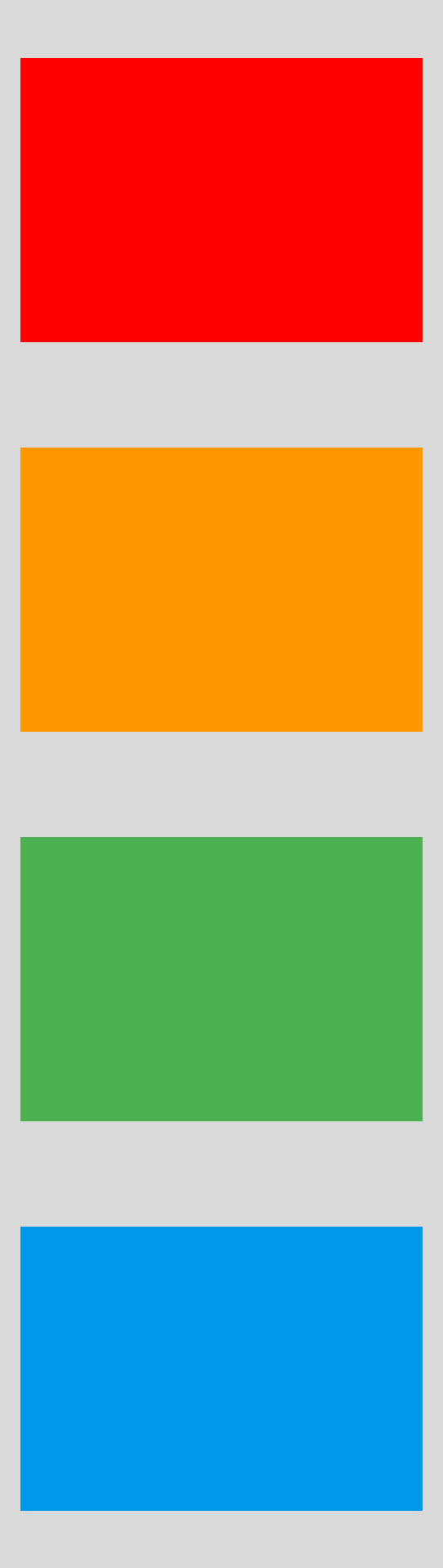